Research Philosophy
Basic or fundamental research
We consider basic research to be the deliberate human action leading to discovery in any field of study and human endeavor. Thus, the “pulse” of basic research can be found at the infinite boundary of the “known” and the “unknown”. In light of the above, the research conducted in the Computational Fracture Mechanics and Composites (CFMC) laboratory represents a “sliver” of potential directions, just like a ray of light emanating from a flashlight pointing in a given direction in the vast darkness of the night. As shown in the schematic above, the lab’s basic research thrust areas include;
- Materials Modeling
- Computational Methods
- Manufacturing Processes and Systems
- Biomechanics
- Technology Transfer
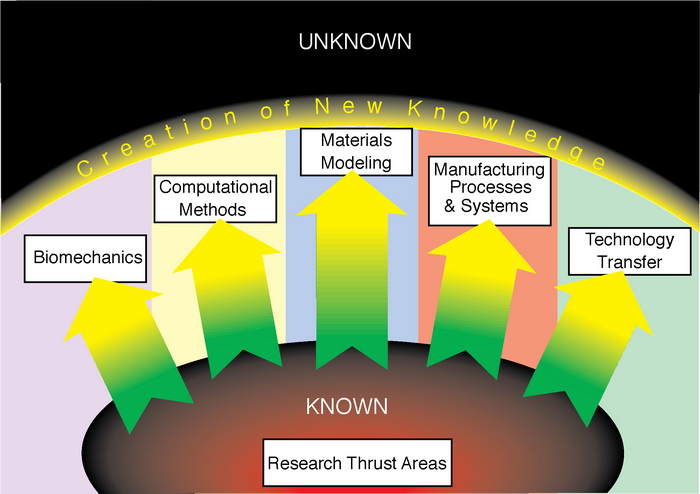
Applied research
We consider applied research to be the deliberated human action leading to the development of “methods”, “processes” and “tools” for the benefit of society. As such, applied research which may utilize the outcomes of basic research forms the foundation in the development of new technologies required for the advancement of the “quality” of human life. The CFMC lab is engaged in applied research in the following areas,
- Health monitoring of structures.
- Software development enabling technology transfer.
Scholarship
We consider scholarship to be the deliberate human action leading to the dissemination of new discoveries, methods, processes and tools thus effectively transforming the “unknown” to “known”. As such, scholarship is a required act in the unfolding of the “envelope of knowledge.” It is the act that documents and informs of the human successes in our incremental efforts to evolve to a better state of being. Thus, scholarship is a foundational pillar of all actions aimed at discovery and innovation for a better society.
In disseminating our basic and applied research findings, we use written (both hard and e-forms) and oral forums that may include peer reviewed journals and periodicals, reports, graduate M.S. and Ph.D. theses, conference presentations, poster exhibits, seminars, formal teaching and person to person communications.
Topics Addressed in the CFMC Laboratory
Researchers in the CFMC laboratory employ theoretical and computational tools and methods in investigating and exploring the forefront of knowledge in several areas of research. Primary focus is given to materials modeling aiming at establishing the functional relationships between micro-structure and macro-mechanical material response and failure. Equal focus is placed on studies of biomaterial interface fracture as it relates to laminated systems and composite materials.
Materials systems studied in the CFMC laboratory include, polycrystalline ceramics, unidirectionally fiber reinforced ceramic and polymer matrix composites, layered composites and composite laminates, particulate composites, woven ceramic and polymer matrix composites and Fibrous Monolith Composites (FMCs). Both linear and non-linear damage evolution studies have been carried out in addressing the effects of stress-induced damage on the system’s mechanical response.
Phenomena investigated include, stress induced micro-cracking damage, toughening and fracture in polycrystalline ceramics, fiber reinforced woven composites and fibrous monolith composites, fracture of bimaterial interfaces, fracture in periodically layered systems, delamination in composite laminates, thin film decohesion and sintering in materials processing.
In addition to the materials research described above, and as shown in the graph, research conducted in the CFMC Laboratory includes the areas of Computational Methods (developing specialized types of finite elements for woven composites and other systems), biomechanics, manufacturing and technology transfer through the development of the homegrown finite element software DENDRO.
Topics listed in the graph below are either actively pursued or have been the focus of past research.
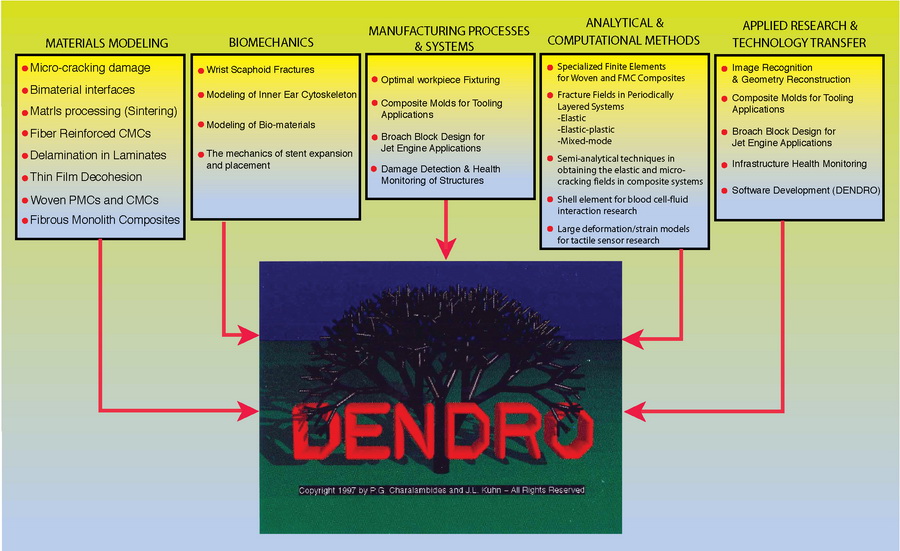
Active Research Projects
Project title:
Development of a large deformation shell element embedded in blood cell-fluid interaction model
Ph.D. Graduate student:
- Ms. Yangling Zhou
Abstract
This research focuses on the development of a specialized shell element capable of modeling blood cell response under large deformation, hyperelastic material response conditions. A specialized material model for cell bio-tissue developed elsewhere is employed along with a non-linear kinematics model in developing the specialized shell element. The development of the element is driven by fluid-blood cell interaction studies aimed at assessing blood-cell microsurface texture interactions required in drag efficacy studies.
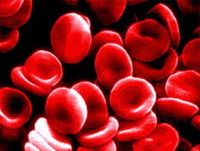
An image of deformed red blood cells during fluid-cell interaction (origin?)
Project title:
Elastomeric layer deformations under applied pressure and shear loadings for tactile sensor applications
Ph.D. Graduate student:
- Mr. Kourosh M. Kalayeh
Abstract
The study is motivated by the need to develop highly sensitivity tactile sensors for both robotic and bionic applications. The ability to predict the response of an elastomeric layer under severe pressure conditions is key to the development of highly sensitive capacitive tactile sensors capable of detecting the location and magnitude of applied forces over a broad range of contact severity and layer depression. Thus, in this work, a large deformation Mooney Rivlin material model is employed in establishing the non-linear mechanics of an elastomeric layer of finite thickness, subjected to uniform displacement control compression. An analytical non-linear model validated numerically via the method of finite elements is developed. Two dimensional, plane strain conditions of an infinitely long and of finite thickness elastomeric layer are assumed. The layer is subjected to a uniform vertical large displacement with symmetry conditions applied at the contact center. Cauchy normal and shear stress profiles as well as displacement profiles are established over a broad range of a layer compression including up to 50% of layer thinning. The relevance of the study to tactile sensing is drawn by using model predictions to determine the relationship between the sensor conducting relatively stiff layers embedded in the polymeric phase and thus its capacitance to the applied load. Implicit in this approach is the assumption that the stiff conducting sensor electrodes embedded in a very soft elastomeric layer follow the deformation contours of the surrounding layer calculated in the absence of the stiff electrodes. In other words, the stiff electrodes can be seen as suspended stiff wires in a “jello” like layer that flow with the layer deformation.
Thus, the model allows for the determination of the non-linear relationship between the relative separation of the conducting electrodes and thus the sensor capacitance during touch, to the force magnitude of the force concentrated at the symmetry plane or sensor center. The current model is expected to further improve the sensitivity and range of polymeric tactile sensors currently under development.
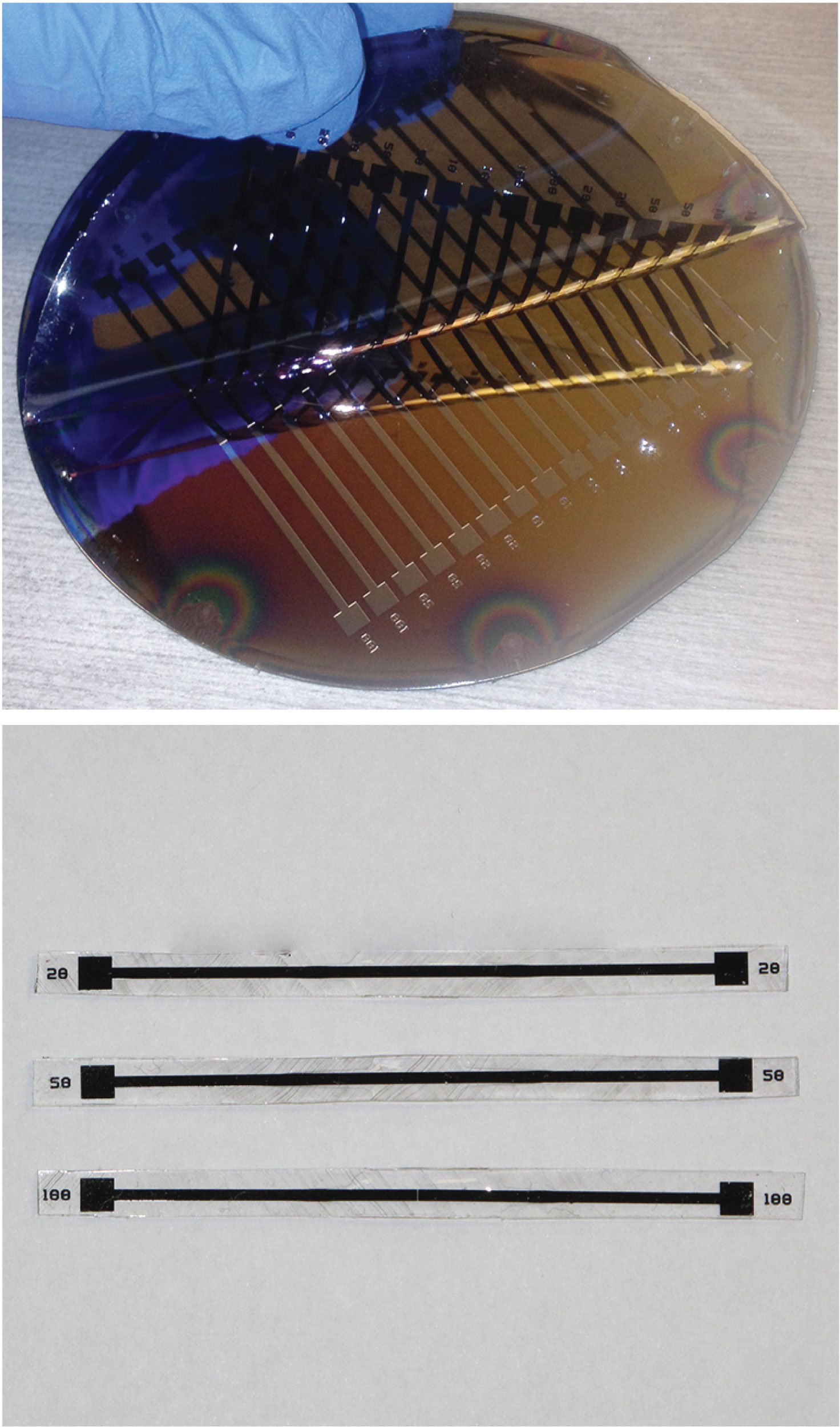
Tactile sensor arrays micro-fabricated at UMCP by Alexi Charalambides and Sarah Bergbreiter.
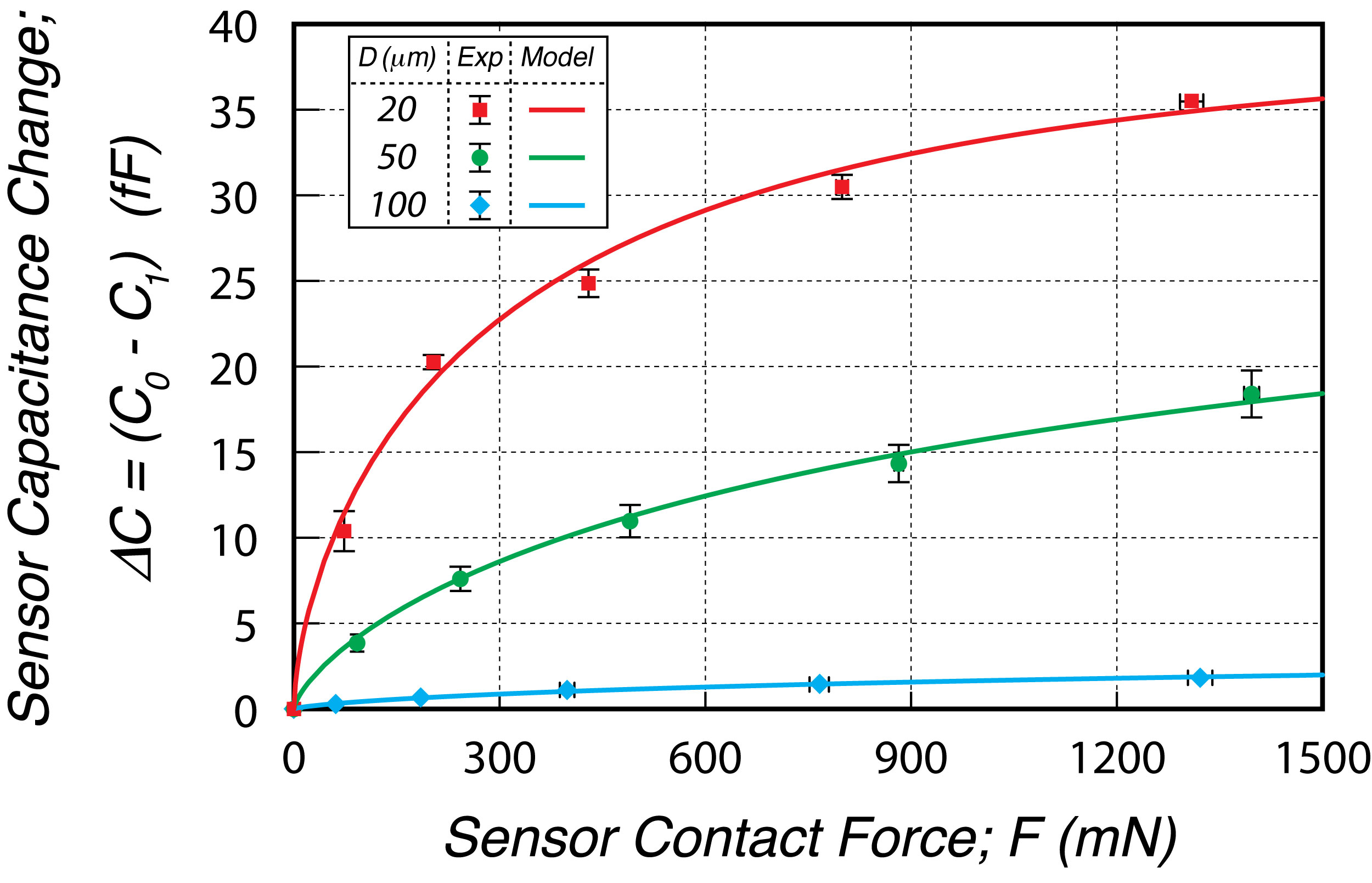
Sensor capacitance change plotted against sensor contact force. The points represent experimental data whereas the solid lines represent analytical model predictions (Recent results).
Project title:
Model and non-model methods for damage and crack detection in structural health assessment and monitoring
Graduate & undergraduate students
- Mr. Oscar Sener (M.S. Candidate)
- Ms. Carolyn Zellhoffer (UG research)
- Dr. Xiaomin Fang (Graduated, Dec. 2013)
- Dr. Valery Aldyeh (Graduated, Dec. 2013)
Abstract
This study addresses the mechanics of “healthy” as well as cracked cantilever beams subjected to a transverse force applied at it’s free end. Static, modal and frequency response as well as time dependent dynamic models are developed. The analytical models are compared to their 2D finite element counterparts. Frequency shifts induced by the presence of the crack are used in the development of frequency and mode shape models for crack detection. As an outcome of the numerical studies, novel non model crack detection methods are proposed utilizing curvature changes on the beam free surfaces induced by the presence of the crack. The effects of shallow as well as well embedded cracks are studied. Informed by the studies on homogeneous cracked beams have, the project is now exploring the effects of heterogeneity present in biomaterial or composite laminates containing delamination cracks. Crack orientation effects are also been studied as needed to extend the outcomes to a broader generation of laminate systems.
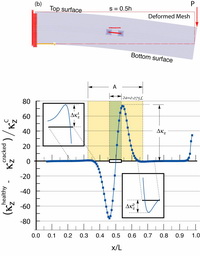
A cracked cantilever beam subjected to an end force static loading. The free surface curvature profile changes predicted along the beam length. (X. Fang, Ph.D. Thesis)
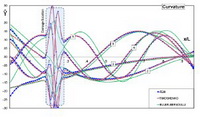
Mode shape free surface curvature profiles of a crack beam. (V. Aladyeh, Ph.D. Thesis)
Recently Sponsored Projects
- Acquisition of A Three-Dimensional Scanning Laser Vibrometer for Research and Education. Co-PI with W.Zhu and J. V. Martins. Funded by The National Science Foundation (NSF).
- Industry Sponsored Capstone Design. Funded by Pratt & Whitney Corporation.
- Mechanical modeling and characterization of fibrous Monolith Composites (FMCs). Funded by Advance Ceramic Composites
- Fundamental Studies in Finite Element Analysis For Computational Materials Science. Funded by The National Institute of Standards and Technology, (NIST).
- Materials and Processes for Integrated High Payoff Propulsion Technology. Subcontract to TAT and CCI, Inc. funded through a U.S. Air-Force PRDA program.